What REALLY Makes Your Custom Watch Case Materials Stand Out?
Let’s be honest – when I first started sourcing cases for boutique watch brands, I underestimated how agonizing material selection could be. It’s not just about looks; it’s about engineering identity. Your case is the armor, the first handshake, the silent ambassador of a brand’s ethos. And for brands like yours partnering with manufacturers (hey, that’s us!), this decision echoes through every step of production.
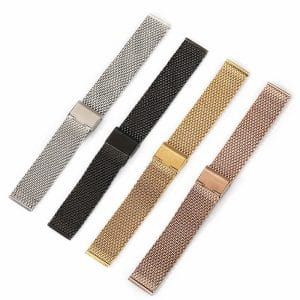
The Material Conundrum in Custom Watchmaking
You’re not just slapping metal together. You’re crafting a legacy. I’ve seen brands lose sleep over balancing aesthetics, durability, MOQs, and that elusive “wow” factor. Remember the Swiss brand that insisted on Grade 5 titanium for a 500-piece run? The machining costs made them sweat, but the featherlight resilience became their signature. That’s the power of intentional custom watch case materials.
Surgical Steel: The Reliable Workhorse
316L stainless steel isn’t glamorous, but my workshop swears by it. Why? It’s like the trusted sous-chef – consistent, corrosion-resistant, and shockingly adaptable. For brands needing 300+ units with complex finishes (brushed, PVD, you name it), steel is pragmatic magic. But here’s the kicker: cheap steel ruins everything. We source hypoallergenic EU-certified billets because a rash on a customer’s wrist kills luxury vibes faster than you can say “return policy”.
Titanium: Where Lightness Meets Grit
Ah, titanium – the dark horse. When a U.S. client demanded cases lighter than their competitor’s carbon fiber models, we suggested Ti. Machining it? A nightmare. The tools scream, the costs spike, but good grief, the result! 45% lighter than steel, virtually scratch-proof, and that muted gunmetal gray? Chef’s kiss. Pro tip: For small-batch custom watch case materials, factor in 20% extra machining time. Trust me, your production manager will thank you.
Ceramic: The Scratch-Proof Maverick
Don’t believe the “fragile” hype. Modern zirconia ceramic is tougher than my morning espresso. I pushed back when a German brand wanted ultra-thin ceramic cases for a pilot series. “It’ll shatter!” I groaned. Six months of R&D later, we shipped cases surviving 1,200°C and diamond-tip scratches. The catch? Color limitations. Jet black or stark white dominates. Want millennial pink? Prepare for glaze chemistry headaches and higher MOQs.
Precious Metals: When Image Is Everything
Gold or platinum cases scream heritage, but let’s talk reality. For OEM projects, I advise clients: Use accents. Solid 18k gold cases skyrocket your BOM cost and attract customs headaches. One client saved 30% by fusing gold bezels onto titanium bodies – same luxe feel, sane logistics. And recycling? We melt scrap for reuse. Sustainability sells in Milan and LA.
The Hidden Player: Surface Finishing
Here’s where many brands drop the ball. Your material choice dictates finishing options. Sandblasted titanium hides micro-scratches. Polished ceramic? Fingerprint central. For a recent yacht-timer project, we combined brushed lugs with polished case sides. Took 12 prototype rounds, but the play of light was worth every minute.
Why Your “Durable Custom Watch Case Materials for Brands” Decision Matters
It impacts everything:
Certifications: Need ISO 6425 dive ratings? Steel or titanium only.
Lead Times: Exotic materials add 4-6 weeks. Plan backward from Baselworld.
Minimums: Ceramic MOQs start at 200 units; steel at 50.
Last month, a startup insisted on “unobtanium” (their word, not mine). We gently steered them toward DLC-coated steel. Saved their budget, met deadlines, kept their design ethos intact. That’s the dance of watch manufacturing materials.
Final Thought: Collaborate Early
The best custom watch case materials choices happen when designers and engineers spar before CAD drawings. Bring us your wildest ideas early. We’ll tell you if bronze will patina unevenly, or if that sapphire case will cost more than your marketing budget. Because honestly? Nothing beats seeing your vision materialize – quite literally – into something timeless.
Ready to experiment? Let’s geek out over metallurgy.